PROCESS COSTING
Process Costing is that aspect of operation costing which is used to ascertain the cost of the product at each process or stage of manufacture. This method of accounting used in industries where the process of manufacture is divided into two or more processes. The objective of process accounting is to find out the total cost of the process and the unit cost of the process for each and every process. Usually the industries where process costing used are textile, oil industries, cement, pharmaceutical etc.
ACCORDING TO CHARTERED INSTITUTE OF MANAGEMENT ACCOUNTANTS, LONDON
“Process costing is that form of operation costing which applies where standardize goods are produced.”
Process costing is a method of costing under which all costs are accumulated for each stage of production or process, and the cost per unit of product is ascertained at each stage of production by dividing the cost of each process by the normal output of that process.
FEATURES OF PROCESS COSTING
Process costing is that aspect of operation costing which is used to ascertain the cost of the product at each process or stage of manufacture, where processes are carried on having one or more of the following features:
CONTINUOUS PROCESS: Production is done having a continuous flow of identical products except where plant and machinery is shut down for repairs, etc.
CLEARLY DEFINED PROCESS: In Process Costing, there is clearly defined process cost centres and the accumulation or all costs (materials, labour and overheads) by the cost centres.
ACCURACY OF RECORDS: The maintenance of accurate records of units and part units produced and cost incurred by each process.
TRANSFER OF MATERIALS: The finished product of one process becomes the raw materials of the next process or operation and so on until the final product is obtained.
TYPES OF LOSSES: Avoidable and unavoidable losses usually arise at different stages of manufacture for various reasons. Treatment of normal and abnormal losses or gains is to be studied in this method of costing.
CHECK ON INEFFICIENCY IS POSSIBLE: Sometimes goods are transferred from one process to another process not at cost price but at transfer price just to compare this with the market price and to have a check on the inefficiency and losses occurring in a particular process. Elimination of profit element from stock is to be learnt in this method of costing.
MEASUREMENT OF PRODUCTION AT EVERY STAGE: In order to obtain accurate average costs, it is necessary to measure the production at various stages of manufacture as all the input units may not be converted into finished goods; some may be in progress. Calculation of effective units is to be learnt in this method of costing.
JOINT PRODUCTS OR BY-PRODUCTS: Different products with or without by-products are simultaneously produced at one or more stages or processes of manufacture. The valuation of by-products and apportionment of joint cost before point of separation is an important aspect of this method of costing. In certain industries, by-products may require further processing before they can be sold. A main product of one firm may be a by-product of another firm and in certain circumstances, it may be available in the market at prices which are lower than the cost to the first mentioned firm. It is essential, therefore, that this cost be known so that advantages can be taken of these market conditions.
UNIFORM OUTPUT: Output is uniform and all units are exactly identical during one or more processes. So the cost per unit of production can be ascertained only by averaging the expenditure incurred during a particular period.
APPLICATIONS OF PROCESS COSTING
The industries in which process costs may be used are many. In fact a process costing system can usually be devised in all industries except where job, batch or unit or operation costing is necessary. In particular, the following are examples of industries where process costing is applied:
1. IDENTICAL PRODUCTS INDUSTRIES
Process costing is most often used when manufacturers release identical products. If mass produced televisions have the same parts, manufacturers can assign consistent prices to the products based on how much the products cost to manufacture overall.
2. INDUSTRIES WITH MULTIPLE DEPARTMENTS
Businesses that have multiple departments usually use process costing so that management can assess the costs accumulated by each department. For example, one department can take the raw resources and refine them before turning them into finished parts, another department can assemble the parts and a third department can test the finished product to assess both quality and safety. Materials might need to be shipped from one department to another, which may incur additional costs. When the costs of production go up unexpectedly, process costing can allow management to quickly pinpoint the department responsible for the increased costs and identify the source of the increased cost.
3. INDUSTRIES WITH INTERCHANGEABLE PARTS
Process costing comes into play when a factory manufactures identical parts. For example, a computer manufacturing plant will create numerous components that are interchangeable among computers of the same model. Process costing allows manufacturers to sell individual parts separately to computer repair shops or individual buyers, since the manufacturers know the cost of the separate parts.
4. INDUSTRIES WITH VARYING PRODUCT FEATURES
Products that have multiple extraneous features can benefit from process costing. Manufacturers can release two versions of the product, with one version costing less but having fewer features and another product costing more but having more features. For example, a manufacturer might release two coffee pots, one with a timer and one without. Process costing lets the manufacturer know how much the timer costs to add to the coffee pot, which enables the manufacturer to gauge how much it must raise the price on the coffee pot with the timer.
5. INNOVATIVE INDUSTRIES
Process costs are important in industries that have high innovation. For example, manufacturers cannot determine an appropriate price for a new type of product without knowing how much the product will cost to manufacture overall. In addition, businesses cannot determine if a product will be profitable until they know the overall cost so they can estimate the maximum price that customers will pay for the product.
GENERAL PRINCIPLES OF PROCESS COSTING
1. The majority of items of cost can ordinarily be identified with specific processes and collected and accumulated separately for each period.
2. Production records of each process are so designed as would show the quantum of production for each period.
3. The total cost of each process is divided by the total production by the process for arriving at the unit cost of the article processed.
4. The cost of any normal spoilage or wastage is included in the cost of the total units produced. Thereby the average cost per unit is increased.
5. As the product travels from one process to another, the cumulative cost thereof in respect of the processes it has already undergone is transferred to the account of the process it has yet to undergo.
ADVANTAGES OF PROCESS COSTING
1. Costs are be computed periodically at the end of a particular period
2. It is simple and involves less clerical work that job costing
3. It is easy to allocate the expenses to processes in order to have accurate costs.
4. Use of standard costing systems in very effective in process costing situations.
5. Process costing helps in preparation of tender, quotations
6. Since cost data is available for each process, operation and department, good managerial control is
possible.
LIMITATIONS OF PROCESS COSTING
1. Cost obtained at each process is only historical cost and are not very useful for effective control.
2. Process costing is based on average cost method, which is not that suitable for performance analysis, evaluation and managerial control.
3. Work-in-progress is generally done on estimated basis which leads to inaccuracy in total cost calculations.
4. The computation of average cost is more difficult in those cases where more than one type of products is manufactured and a division of the cost element is necessary.
5. Where different products arise in the same process and common costs are prorated to various costs units. Such individual products costs may be taken as only approximation and hence not reliable.
ACCOUNTING FOR PROCESS COSTING
ACCOUNTING FOR MATERIALS
Materials and supplies as in the case of job costing are issued to each process only against authorized requisitions. At the end of each process or of each costing period, the requisitions are sorted according to processes and their values listed on a material summary sheet. On the basis of this summary sheet, a journal entry is passed to debit the various process accounts and the material control account is credited.
ACCOUNTING FOR LABOUR
In order to account for labour, the first step is identification of each worker with the process in which he is engaged. If the workers are permanently assigned to the process, such identification would not pose any problem as the pay rolls would be prepared in a manner so as to show the wages cost of each process separately.
Where it is necessary to frequently transfer workers from one process to another, it may not be possible to have a permanent classification of workers according to processes. In such a case, it is necessary to prepare daily time reports showing the number of employees engaged in each process.
If any worker is required to divide his time among two or more processes, a transfer form would be used to record his times on different processes. At the end of the week or that of the costing period, the daily time reports and transfer forms would be abstracted on a labour summary sheet.
On this basis a journal entry would be made, debiting various process accounts and crediting the wages control account.
ACCOUNTING FOR OVERHEADS
Since normally it is practicable to identify all materials and labour charges with specific processes, the overhead expenses chargeable to a process ordinarily would not contain cost of indirect materials or labour.
But there still would be several items of expenses that do not relate to any particular process. It would be necessary to apportion them to various processes on suitable bases. Different bases that are generally adopted for making such a distribution are stated below:
ITEMS OF EXPENSES | BASIS OF DISTRIBUTION |
Rent, rates and taxes | Area occupied by each process. |
Power | Meter readings or horse power of plant employed for each process. |
Fire insurance | Value of asset and the degree of risk involved. |
Water, gas, steam, etc. | Meter readings or technical estimates. |
Depreciation of plant | Value of assets employed. |
Amounts of manufacturing overheads are, usually debited in totals to a total overhead account entitled ‘Manufacturing Overhead Control Account’. From this account, the total amount is distributed to various process accounts on the basis of a manufacturing overhead summary sheet.
The summary sheet contains a description of various items of manufacturing overheads and the manner in which the same has been distributed, i.e. one or other based mentioned above.
PROCESS ACCOUNT
For each process an individual process account is prepared. Each process of production is treated as a distinct cost centre.
Items on the Debit side of Process Account
In process Costing, individual process Accounts are prepared for each process. Each process account is debited with-
(a) Cost of materials used in that process.
(b) Cost of labour incurred in that process.
(c) Direct expenses incurred in that process.
(d) Overheads charged to that process on some pre determined.
(e) Cost of ratification of normal defectives.
(f) Cost of abnormal gain (if any arises in that process)
Items on the Credit side of Process Account
Each process account is credited with-
(a) Scrap value of Normal Loss (if any) occurs in that process.
(b) Cost of Abnormal Loss (if any occurs in that process)
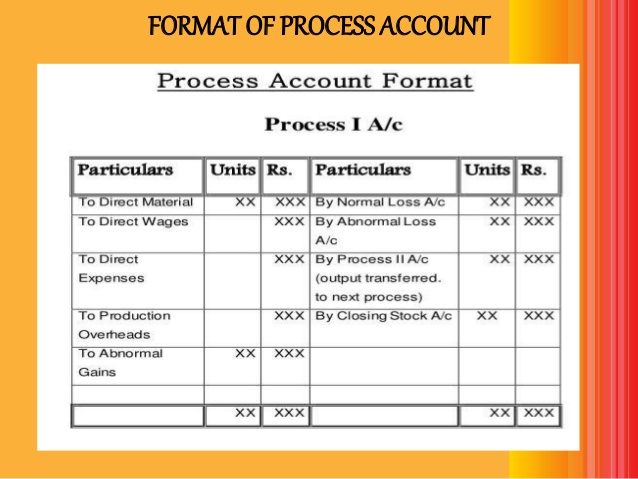
COST OF PROCESS
The cost of the output of the process (Total Cost less Sales value of scrap) is transferred to the next process. The cost of each process is thus made up to cost brought forward from the previous process and net cost of material, labour and overhead added in that process after reducing the sales value of scrap. The net cost of the finished process is transferred to the finished goods account. The net cost is divided by the number of units produced to determine the average cost per unit in that process.
PROCESS LOSSES
In manufacturing processes, entire input is not getting converted into output. A certain part of input is lost while processing which is inevitable. Certain production techniques are of such a nature that some loss is inherent to the production. Wastages of material, evaporation of material are un- avoidable in some process. But sometimes the Losses are also occurring due to negligence of Labourer, poor quality raw material, poor technology etc. These are normally called as avoidable losses. Basically process losses are classified into two categories (a) Normal Loss (b) Abnormal Loss
- Normal Loss:
Normal loss is an unavoidable loss which occurs due to the inherent nature of the materials and production process under normal conditions. It is normally estimated on the basis of past experience of the industry. It may be in the form of normal wastage, normal scrap, normal spoilage, and normal defectiveness. If the normal loss units can be sold as a scrap then the sale value is credited with process account. If some rectification is required before the sale of the normal loss, then the cost of rectification is debited in the process account. The cost per unit of a process is calculated after adjusting the normal loss. In case of Normal Loss the cost per unit is calculated by the under given formulae.
Cost of Good Unit = (Total Cost-Sale value of Scrap/ Input Normal- Loss Units)
- Abnormal Loss:
Any loss caused by unexpected abnormal conditions such as plant breakdown, substandard material, carelessness, accident etc. such losses are in excess of pre-determined normal losses. This loss is basically avoidable. Thus abnormal losses arrive when actual losses are more than expected losses. Abnormal losses in calculated as per under given formulae:
Value of Abnormal Loss = (Total Cost-Sale value of Scrap/ Input Normal- Loss Units) × Units in abnormal loss
Abnormal Process loss should not be allowed to affect the cost of production as it is caused by abnormal (or) unexpected conditions. Such loss representing the cost of materials, labour and overhead charges called abnormal loss account. The sales value of the abnormal loss is credited to Abnormal Loss Account and the balance is written off to costing P & L A/c.
SPECIMEN: ABNORMAL LOSS ACCOUNT
PARTICULARS | UNITS | AMOUNT | PARTICULARS | UNITS | AMOUNT |
To Process A/c | By Bank Account | ||||
By Costing Profit and Loss Account | |||||
ABNORMAL GAINS
The margin allowed for normal loss is an estimate (i.e. on the basis of expectation in process industries in normal conditions) and slight differences are bound to occur between the actual output of a process and that anticipates. This difference may be positive or negative. If it is negative it is called ad abnormal Loss and if it is positive it is Abnormal gain i.e. if the actual loss is less than the normal loss then it is called as abnormal gain. The value of the abnormal gain calculated in the similar manner of abnormal loss. The formula used for abnormal gain is:
Value of Abnormal Gain = (Normal cost of normal output x Units of Abnormal gain)/ Normal output
Normal cost of normal output = Total expenditure– Sale Proceeds of scrap
Normal output = Input – Units of normal loss
Units of Abnormal gain = Normal loss- Actual loss
Or = Actual output – Normal output
The sales values of abnormal gain units are transferred to Normal Loss Account since it arrive out of the savings of Normal Loss. The difference is transferred to Costing P & L A/c. as a Real gain.
SPECIMEN: ABNORMAL GAIN ACCOUNT
PARTICULARS | UNITS | AMOUNT | PARTICULARS | UNITS | AMOUNT |
To Normal Loss A/c | By Process Account | ||||
To Costing Profit and Loss Account | |||||
EQUIVALENT PRODUCTION
This represents the production of a process in terms of completed units. In other words it means converting the incomplete production units into its equivalent of complete units. In each process an estimate is made of the percentage completion of any work-in-progress. A production schedule and a cost schedule will then be prepared. The work-in-progress is inspected and an estimate is made of the degree of completion, usually on a percentage basis. It is most important that this estimate is as accurate as possible because a mistake at this stage would affects the stock valuation used in the preparation of final accounts. The formula for equivalent production is:
Equivalent units of work-in-progress = Actual no. of units in process of manufacture x Percentage of work completed
For example: If 20% work has been done on the average of 1,000 units still in process, then 1,000 such units will be equal to 200 completed units. The cost of work-in-progress will be equal to 200 completed units.