PROCESS COSTING VS JOB COSTING
Process Costing vs Job Costing is as follows:
JOB COSTING
Job costing or job order costing also called specific order costing is a method of costing which is used when work is undertaken as per the customer’s special requirement (tailor-made).
ACCORDING TO INSTITUTE OF COST AND MANAGEMENT ACCOUNTANTS, LONDON
“Job costing is that form of specific order costing which applies where work is undertaken to customer’s specific requirements and each order is of comparatively of short duration.”
Under this method of costing, each job is considered to be a distinct cost unit. As such, each job is separately identifiable. In the case of a job, work is usually carried out within the factory or workshop. Sometimes, a job is accomplished even in the customer’s premises.
Job costing is employed in the following cases:
- Where the production is against the order of the customer or jobs are executed for different customers according to their specifications.
- Where each job needs special treatment and no two orders are necessarily alike.
- Where there is no uniformity in the flow of production from one department to another.
- Where the work-in-progress differs from period to period on the basis of the number of jobs in hand.
Job costing is applicable to printing, furniture, hardware, ship-building, heavy machinery, foundry general engineering works, machine tools, interior decoration, repairs and other similar work.
PROCESS COSTING
Process costing is that aspect of operation costing which is used to ascertain the cost of the product at each process or stage of manufacture. This method of accounting used in industries where the process of manufacture is divided into two or more processes. The objective is to find out the total cost of the process and the unit cost of the process for each and every process. Usually the industries where process costing used are textile, oil industries, cement, pharmaceutical etc.
ACCORDING TO CHARTERED INSTITUTE OF MANAGEMENT ACCOUNTANTS, LONDON
“Process costing is that form of operation costing which applies where standardize goods are produced”
Process costing is a method of costing under which all costs are accumulated for each stage of production or process, and the cost per unit of product is ascertained at each stage of production by dividing the cost of each process by the normal output of that process.
Process Costing vs Job Costing is as follows:
BASIS FOR COMPARISON | JOB COSTING | PROCESS COSTING |
MEANING | Job costing refers to calculating the cost of a special contract, work order where work is performed as per client’s or customer’s instructions. | A costing method, in which the costs which are charged to various processes and operations is ascertained, is known as Process Costing. |
NATURE | Job Costing involves Customized production. | Process Costing involves Standardized production. |
ASSIGNMENT OF COST | The cost of each job is calculated separately. | First of all, cost is determined for the process, thereafter spread over the produced units. |
COST CENTER | Job is the cost centre in job costing. | Process is the cost center in process costing. |
CONTROL | As each product unit is different and production is not continuous, proper control is comparatively difficult. | As the production is standardized and stable, control is comparatively easier. |
SCOPE OF COST REDUCTION | The scope of cost reduction in job costing is less. | The scope of cost reduction in job costing is high. |
TRANSFER OF COST | No transfer of cost is made from one job to another job. | Cost is transferred from one process to another. |
IDENTITY | Each job is different from another. | Products are manufactured consecutively and so they lose their identity. |
COST ASCERTAINMENT | The cost is ascertained after the Completion of the job. | The cost is ascertained at the End of the cost period. |
INDUSTRY TYPE | Job costing is suitable for the industries which manufactures products as per customer’s order | Process costing is perfect for the industry where mass production is done. |
LOSSES | Losses are usually not segregated. | Normal losses are carefully ascertained and abnormal losses are bifurcated. |
WORK-IN-PROGRESS (WIP) | WIP may or may not exist at the beginning or at the end of the financial year. | WIP will always be present in the beginning or at the end of the accounting period. |
SIZE OF JOB | Used for small production units. | Used for large production units. |
RECORD KEEPING | The record keeping is Tedious task in job costing. | The record keeping is an Efficient task in process costing. |
CONCLUSION
There is no comparison between Job Costing and Process Costing because both the methods are used in different industries. Although, the differences exist in the two methods. One such difference is, each job requires a high degree of supervision and control, but the process does not require so, as they are standardized in nature.
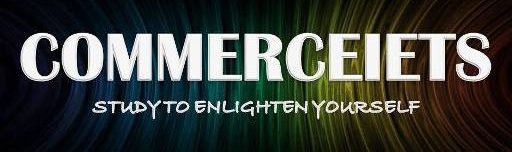