Traditional Costing Vs ABC Costing
The difference between Traditional costing vs ABC costing is as follows:
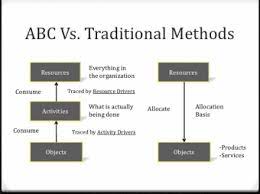
BASIS OF DIFFERENCE | TRADITIONAL COSTING | ACTIVITY BASED COSTING |
MEANING | Traditional costing is the allocation of factory overhead to products based on the volume of production resources consumed. | The Activity-Based Costing (ABC) is a costing system, which focuses on activities performed to produce Products. ABC is that costing in which costs are first traced to activities and then to products. |
COST POOLS | Traditional costing system accumulates costs into facility-wise or departmental cost pools. The costs in each cost pool are heterogeneous- they are costs of many major processes and generally are not caused by a single factor. | ABC system accumulates costs into activity cost pools. These are designed to correspond to major activities or business processes. By design, the costs in each cost pool are largely caused by single factor- the cost driver. |
ALLOCATION BASES | Traditional systems allocate costs to products using volume-based allocation bases: units, direct labor input, machine hours, revenue etc. | ABC system allocates costs to products, services and other cost objects from the activity cost pools using allocation bases corresponding to the cost drivers of activity costs. |
HIERARCHY OF COSTS | This costing generally estimates all the costs of an organization as being driven by the volume of product or service delivered. | ABC allows for non- linearity of costs within the organization by explicitly recognizing that some costs is not caused by the number of units produced. |
COST OBJECTS | Traditional Costing focuses on estimating the cost of a single cost object i.e. unit of product or service. | ABC focuses on estimating the costs of many cost objects of interest: units, batches, product lines, business processes, customers and suppliers. |
DECISION SUPPORT | Because of the inability to align allocation bases with cost drivers, leads to the problems of over casting and under casting of costs. | Because of the ability to align allocation bases with cost drivers, provides more accurate information to support managerial decisions. |
COST CONTROL | Cost control is viewed as a departmental exercise rather than a cross functional effort. | By providing summary costs of the organizational activities, ABC allows for prioritization of cost management efforts. |
COSTING SYSTEM | Traditional costing system is relatively less expensive to implement and maintain. | ABC system is expensive to implement and maintain. |
SUITABILITY | Traditional costing is suitable for labor intensive and low overhead companies. | Activity based costing system is suitable for capital-intensive, product-diverse, widely diverse set of operating activities, variation in numbers of production runs, high-overhead companies. |
TYPES OF ACTIVITIES | Only two types of activities viz. Unit Level Activities and Facility Level Activities are identified. | All levels of activities in the manufacturing cost hierarchy viz. Unit Level, Batch Level, Product Level and Facility Level are identified. |
OVERHEAD RATES | Overhead Rates can be used to ascertain cost of products only. | Activity Cost Driver Rates can be used to ascertain cost of products and also cost of other cost objects such as customer segments, distribution channels. etc. |
TRADITIONAL COSTING
Traditional costing is the allocation of factory overhead to products based on the volume of production resources consumed. Under this method, overhead is usually applied based on either the amount of direct labor hours consumed or machine hours used. The trouble with traditional costing is that factory overhead may be much higher than the basis of allocation, so that a small change in the volume of resources consumed triggers a massive change in the amount of overhead applied. This is a particularly common issue in highly automated production environments, where factory overhead is quite large and direct labor is close to nonexistent.
ACTIVITY BASED COSTING
The Activity-Based Costing (ABC) is a costing system, which focuses on activities performed to produce Products. ABC is that costing in which costs are first traced to activities and then to products.
Activity-based costing (ABC) is mostly used in the manufacturing industry since it enhances the reliability of cost data, hence producing nearly true costs and better classifying the costs incurred by the company during its production process.
CONCLUSION
Activity-based costing was developed to circumvent this issue with traditional costing, using a more detailed analysis of the relationship between overhead costs and cost drivers. Many cost drivers may be used to create a more well-founded allocation of overhead costs.
Traditional costing still works well for financial statement reporting, where it is simply intended to apply overhead to the number of produced units for the purpose of valuing ending inventory. There is no consequence from a management decision-making perspective.
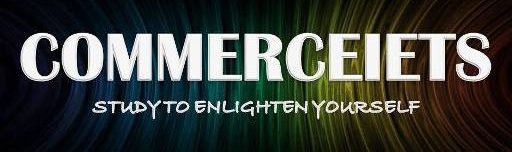