BATCH COSTING
Batch Costing is that form of specific order costing under which each batch is treated as a cost unit and costs are accumulated and ascertained separately for each batch. Each batch consists of a number of like units. In this system, a group of identical units, comprising of a batch is used as a cost unit, to estimate cost. To ascertain the cost per unit, the total cost of the batch is divided by the number of units produced in a batch. Batch costing is applied in industries where identical products are produced.
FEATURES OF BATCH COSTING
- A batch is a cost unit which consists of a separate, readily identifiable group of product units which maintains its separate identity throughout the production process.
- The output of batch consists of a number of units and it is not economical to ascertain cost of every unit of output independently.
- Each batch is treated a job and costs are calculated for total batch.
- On completion of production cost per unit is found as
Cost per unit = Total Batch Cost/ Total Units in Batch
- A separate Batch Cost Sheet is used for each batch and is assigned a certain number by which the batch is identified.
TYPES OF COSTS IN BATCH COSTING
There are two types of costs involved in Batch Costing:
(i) Set up costs
(ii) Carrying costs.
If the batch size is increased, set up cost per unit will come down and the carrying cost will increase. If the batch size is reduced, set up cost per unit will increase and the carrying cost will come down. Economic Batch quantity will balance both these opponent costs.
APPLICATIONS OF BATCH COSTING
Batch costing is used for calculating total cost of each batch. Batch is small group of units which is produced for production purposes. We also identify batch of units in our production. All raw materials are supplied on batch basis and other expenses are also paid on the basis of each batch.
Batch Costing is applied in those industries where the similar articles are produced in definite batches for internal consumption in the production of finished products or for sale to customers generally. It is generally applied in –
- Read made Garments Manufacturing Industries
- Pharmaceutical/ Drug Industries
- Spare parts and Components Manufacturing Industries
- Toys Manufacturing Industries
- Tyre and Tubes Manufacturing Industries.
BATCH COSTING ACCOUNTING SOURCE DOCUMENTS
Costs are transferred to the work in process account using the following accounting source documents.
Material Requisition Form
The materials requisition form is used to issue materials either directly to a batch (direct materials) or to production overheads (indirect materials). The transfer takes place by a credit entry to raw materials and a debit entry to either the batch cost sheet or to production overhead.
Batch Timesheet
The batch timesheet is used to transfer labor costs either directly to a batch (direct labor) or to production overheads (indirect labor). The transfer takes place by a credit entry to labor costs and a debit entry to the batch cost sheet or to production overheads.
Production Overhead
Production overhead is accumulated in the production overhead account and comprises indirect materials from the material requisition form, indirect labor from the timesheet and other production overhead such as expenses and depreciation supported by the appropriate source document.
Production overhead is applied to batches using predetermined overhead rate calculated
on an appropriate basis such as direct labor hours or labor cost. The transfer
entry is a credit to production overhead and a debit entry to the batch cost
sheet.
ADVANTAGES OF BATCH COSTING
Following are the main advantages of batch costing as compared to job costing:
- Accounting work is reduced under batch costing because costing is done in respect of a batch of product of homogeneous jobs.
- It makes benefit of reduced cost of production arising out of economic batch quantity or lot size.
- Under this method, supervision becomes easy and more effective by means of spreading over the supervisor’s time over all the units constituting the batch. Thus, the idle time of supervisor’s as well as workers are eliminated.
- The loss of time under job costing arising out of inter-job transfer of materials, labours and tools are minimized under batch costing.
- There are the advantages of consistent cost of production of every article produced in a batch under batch costing.
DISADVANTAGES OF BATCH COSTING
The main disadvantages of batch costing are:
- Determination of a batch from various jobs often pose problem. It is difficult to come across absolute homogeneity of jobs.
- When quantity of goods to be manufactured differs from customer to customer, again it becomes difficult to determine the batch.
- If the production of a batch is wrongly undertaken, the whole batch of the articles are to be discarded which will become a great loss to the manufacturer.
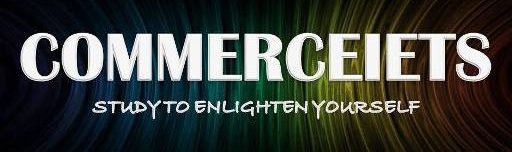