ACTIVITY BASED COSTING
The Activity-Based Costing (ABC) is a costing system, which focuses on activities performed to produce Products. ABC is that costing in which costs are first traced to activities and then to products.
ACCORDING TO CHARTERED INSTITUTE OF MANAGEMENT ACCOUNTANTS, LONDON
“Activity Based Costing is cost attribution to cost units on the basis of benefit received from indirect activities e.g. ordering, setting up, assuring quality.”
ACCORDING TO COKINS
“Activity Based Costing system is the mathematics used to reassign costs accurately to cost objects, that is, outputs, products, services, and customers. Its primary purpose is for profitability analysis.”
ACCORDING TO TURNEY
“ABC refers to a methodology that measures the cost and performance of activities, resources and cost objects. It assigns costs to activities based on their consumption of resources and then allocates costs to cost objects based on their required activities”.
ACCORDING TO THE COMPUTER AIDED MANUFACTURING-INTERNATIONALS (CAM-I)
“Activity Based Costing system in its glossary as a method that measures the cost and performance of process related activities and cost objects, through the assignment of costs to activities, and cost to cost objects.”
ACCORDING TO SWENSONS
“Activity Based Costing system is an information system that assists with decision making, essentially a decision- support system.”
ACCORDING TO CHARLES T HORNGREEN
“Activity Based Costing system is a method that refines a costing system by identifying individual activities as the fundamental cost objects.”
Activity-based costing (ABC) is mostly used in the manufacturing industry since it enhances the reliability of cost data, hence producing nearly true costs and better classifying the costs incurred by the company during its production process.
TERMINOLOGY UNDER ACTIVITY BASED COSTING
1. A Cost Object: It is an item for which cost measurement is required e.g. Product, job or a customer.
2. A Cost Driver: In an Activity Based Costing system, the allocation basis that are used for applying costs to services or procedures are called cost drivers. It is a factor that causes a change in the cost of an activity.
3. Unit level cost: Traditionally, cost drivers were viewed only at the unit level. These drivers create unit-level costs meaning that they are caused by the production or acquisition of a single unit of product or the delivery of a single unit or service.
4. Batch level cost: Costs are caused by a group of things being made, handled or processed at a single time are referred to as batch level costs.
5. Product-level cost: A cost caused by the development, production or acquisition of different items is called a product level or process level cost. These include engineering change orders, equipment maintenance, product development and scrap, if related to product design.
6. Facility-level cost: Some costs cannot be related to a particular product line. These are instead related to providing a facility. For e.g. Cost of maintaining a building or plant security or advertisement promoting the organization.
7. Organizational-level cost: Certain costs are incurred at organizational level for the single purpose of supporting continuing facility operations. These organizational level costs are common to many different activities and products and services can be prorated among services and products on an arbitrary basis only. These costs are not product related .thus they should be subtracted from net product revenues instead of an arbitrary and illogical apportionment.
8. Cost Pool: Costs are grouped into pools according to the activities, which drive them. Example: Costs associated with procurement i.e. ordering, inspection, storing etc would be included in this cost pool and cost driver identified.
FEATURES OF ACTIVITY BASED COSTING
The features of Activity Based Costing are as under:
• Activity-based costing (ABC) is a two-stage product costing method that first assigns costs to activities and then allocates them to products based on the each product’s consumption of activities.
• An activity is any discrete task that an organization undertakes to make or deliver a product or service.
• Activity-based costing is based on the concept that products consume activities and activities consume resources.
• Activity-based costing can be used by any organization that wants a better understanding of the costs of the goods and services it provides, including manufacturing, service, and even non-profit organizations.
PROCESS OF ACTIVITY BASED COSTING
Step 1. IDENTIFY RESOURCES
Resources represent the expenditure of an organization. These are the same costs that are represented in a traditional accounting, Activity Based Costing links these cost to products, customers or services.
Step2. IDENTIFY ACTIVITIES
Activities represent the work performed in an organization. ABC accounts for the costs based on what activities caused them to occur. By determining the actual activities that occur in various departments it is then possible to more accurately relate these costs to customers, products and services. Activities comprise of units of work or tasks.
For example, purchase of materials is an activity consisting a series of tasks like purchase requisition, advertisement inviting quotations, identification of suppliers, placement of purchase order, follow-up etc.
Types of Activities: Activities basically fall into four different categories, known as the manufacturing cost hierarchy. These categories were first identified by Cooper in 1990 and help to determine the type of activity cost driver required. The categories are:
Unit level activities: These are activities for which the consumption of resources can be identified with the number of units produced. It is performed each time a unit is produced. | Use of indirect materials/consumables. |
Batch level activities: The costs of some activities are driven by the number of batches of units produced. These are activities related to setting up of a batch or a production run. It is performed each time a batch is processed. | Material ordering, Inspection of Products. |
Product level activities: The cost of some activities are driven by the creation of a new product line and its maintenance. | Designing the product, Producing parts specifications and keeping technical drawings of products. |
Facility Level Activities: It must be carried out regardless of which products are produced. These are activities necessary for sustaining the manufacturing process and cannot be directly attributed to individual products | Plant Security, Production Manager’s Salary and Maintenance of buildings. |
Step 3. IDENTIFY COST OBJECTS
Activity Based Costing provides profitability by one or more cost object. Cost object profitability is utilized to identify money losing customers to validate separate divisions or business units. Defining outputs to be reviewed is an important step in a successful Activity Based Costing implement action.
Step 4. DETERMINE RESOURCE DRIVERS
Resource drivers provide the link between the expenditure of an Organisation and activities performed within the Organisation.
Step 5. DETERMINE COST (ACTIVITY) DRIVERS
Determination of cost drivers completes the last stage of the model. Cost drivers trace or links the cost of performing certain activities to cost objects.
Activity Cost Driver Rate = Activity Cost Driver / Total Cost of Activity(Cost pool)
Step 6. ASSIGN COSTS TO THE COST OBJECTS
The following formula can be used for assigning costs to the cost objects:
Costs = Resources Consumed × Activity Cost Driver Rate
OBJECTIVES OF ACTIVITY BASED COSTING
The objectives of Activity-based Costing are discussed below:
- To remove the distortions in computation of total costs as seen in the traditional costing system and bring more accuracy in the computation of costs of products and services.
- To help in decision making by accurately computing the costs of products and services.
- To identify various activities in the production process and further identify the value adding activities.
- To distribute overheads on the basis of activities.
- To focus on high cost activities.
- To identify the opportunities for improvement and reduction of costs.
- To eliminate non value adding activities.
ADVANTAGES OF ACTIVITY BASED COSTING
The fundamental advantage of using an ABC system is to more precisely determine how overhead is used. Once you have an Activity Based Costing system, you can obtain better information about the following issues:
- Activity costs: Activity Based Costing is designed to track the cost of activities, so you can use it to see if activity costs are in line with industry standards. If not, Activity Based Costing is an excellent feedback tool for measuring the ongoing cost of specific services as management focuses on cost reduction.
- Customer profitability: Though most of the costs incurred for individual customers are simply product costs, there is also an overhead component, such as unusually high customer service levels, product return handling, and cooperative marketing agreements. An ABC system can sort through these additional overhead costs and help you determine which customers are actually earning you a reasonable profit. This analysis may result in some unprofitable customers being turned away, or more emphasis being placed on those customers who are earning the company its largest profits.
- Distribution cost: The typical company uses a variety of distribution channels to sell its products, such as retail, Internet, distributors, and mail order catalogs. Most of the structural cost of maintaining a distribution channel is overhead, so if you can make a reasonable determination of which distribution channels are using overhead, you can make decisions to alter how distribution channels are used, or even to drop unprofitable channels.
- Make or buy: ABC provides a comprehensive view of every cost associated with the in-house manufacture of a product, so that you can see precisely which costs will be eliminated if an item is outsourced, versus which costs will remain.
- Margins: With proper overhead allocation from an ABC system, you can determine the margins of various products, product lines, and entire subsidiaries. This can be quite useful for determining where to position company resources to earn the largest margins.
- Minimum price: Product pricing is really based on the price that the market will bear, but the marketing manager should know what the cost of the product is, in order to avoid selling a product that will lose a company money on every sale. Activity Based Costing is very good for determining which overhead costs should be included in this minimum cost, depending upon the circumstances under which products are being sold.
- Production facility cost: It is usually quite easy to segregate overhead costs at the plant-wide level, so you can compare the costs of production between different facilities.
DISADVANTAGES OF ACTIVITY BASED COSTING
Many companies initiate Activity Based Costing projects with the best of intentions, only to see a very high proportion of the projects either fail or eventually lapse into disuse. There are several reasons for these issues, which are:
- Cost pool volume: The advantage of an Activity Based Costing system is the high quality of information that it produces, but this comes at the cost of using a large number of cost pools – and the more cost pools there are, the greater the cost of managing the system. To reduce this cost, run an ongoing analysis of the cost to maintain each cost pool, in comparison to the utility of the resulting information. Doing so should keep the number of cost pools down to manageable proportions.
- Installation time: ABC systems are notoriously difficult to install, with multi-year installations being the norm when a company attempts to install it across all product lines and facilities. For such comprehensive installations, it is difficult to maintain a high level of management and budgetary support as the months roll by without installation being completed. Success rates are much higher for smaller, more targeted ABC installations.
- Multi-department data sources: An Activity Based Costing system may require data input from multiple departments, and each of those departments may have greater priorities than the ABC system. Thus, the larger the number of departments involved in the system, the greater the risk that data inputs will fail over time. This problem can be avoided by designing the system to only need information from the most supportive managers.
- Project basis: Many Activity Based Costing projects are authorized on a project basis, so that information is only collected once; the information is useful for a company’s current operational situation, and it gradually declines in usefulness as the operational structure changes over time. Management may not authorize funding for additional Activity Based Costing projects later on, so ABC tends to be “done” once and then discarded. To mitigate this issue, build as much of the ABC data collection structure into the existing accounting system, so that the cost of these projects is reduced; at a lower cost, it is more likely that additional Activity Based Costing projects will be authorized in the future.
- Reporting of unused time: When a company asks its employees to report on the time spent on various activities, they have a strong tendency to make sure that the reported amounts equal 100% of their time. However, there is a large amount of slack time in anyone’s work day that may involve breaks, administrative meetings, playing games on the Internet, and so forth. Employees usually mask these activities by apportioning more time to other activities. These inflated numbers represent misallocations of costs in the ABC system, sometimes by quite substantial amounts.
- Separate data set: An ABC system rarely can be constructed to pull all of the information it needs directly from the general ledger. Instead, it requires a separate database that pulls in information from several sources, only one of which is existing general ledger accounts. It can be quite difficult to maintain this extra database, since it calls for significant extra staff time for which there may not be an adequate budget. The best work-around is to design the system to require the minimum amount of additional information other than that which is already available in the general ledger.
- Targeted usage: The benefits of ABC are most apparent when cost accounting information is difficult to discern, due to the presence of multiple product lines, machines being used for the production of many products, numerous machine setups, and so forth – in other words, in complex production environments. If a company does not operate in such an environment, then it may spend a great deal of money on an ABC installation, only to find that the resulting information is not overly valuable.
CHARACTERISTICS OF SUCCESSFUL ABC IMPLEMENTATIONS
(1) Strong Top Management Support
Without leadership from top management, some managers may not see any reason to change nor consider the ABC implementation as important.
(2) Should Have Cross-Functional Involvement
ABC cannot be alone done by Finance or Costing Department. A well designed ABC system requires intimate knowledge of many parts of an organization hence involved those employees who have the in-depth working knowledge and those who ae familiar with the various parts of an organization’s operations.
(3) ABC data should be linked to how people are evaluated and rewarded.
With the implementation of the ABC, it’s crucial that the evaluation of employee evaluation should derive from ABC data, it should not come out from other existing traditional costing system. Otherwise, this will send a wrong message that ABC data is unimportant and can even be ignored.
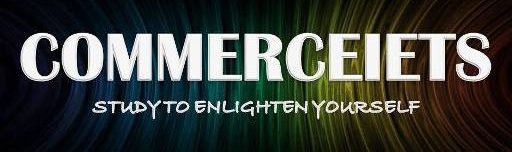