JOB COSTING
Job costing or job order costing also called specific order costing is a method of costing which is used when work is undertaken as per the customer’s special requirement (tailor-made).
ACCORDING TO INSTITUTE OF COST AND MANAGEMENT ACCOUNTANTS, LONDON
“Job costing is that form of specific order costing which applies where work is undertaken to customer’s specific requirements and each order is of comparatively of short duration.”
Under this method of costing, each job is considered to be a distinct cost unit. As such, each job is separately identifiable. In the case of a job, work is usually carried out within the factory or workshop. Sometimes, a job is accomplished even in the customer’s premises.
Job costing is employed in the following cases:
- Where the production is against the order of the customer or jobs are executed for different customers according to their specifications.
- Where each job needs special treatment and no two orders are necessarily alike.
- Where there is no uniformity in the flow of production from one department to another.
- Where the work-in-progress differs from period to period on the basis of the number of jobs in hand.
Job costing is applicable to printing, furniture, hardware, ship-building, heavy machinery, foundry general engineering works, machine tools, interior decoration, repairs and other similar work.
FEATURES
1. Each job has its own characteristics, depending up on the special order placed by the customer.
2. Each job is treated as a cost unit.
3. A separate job cost sheet is made out for each job on the basis of distinguishing numbers.
4. A separate work in progress ledger is maintained for each job.
5. The duration of the job is normally a short period.
6. Profit or loss is determined for each job independently of others.
ADVANTAGES OF JOB COSTING
The following are the advantages of Job costing:
HELPS IN PREPARING PRICE QUOTATIONS
It helps management to detect which jobs are profitable and which are not. Estimates of cost for similar work in the future may be conveniently made on the basis of accurate record of job costs. This assists in the prompt furnishing of price quotations for specific jobs.
HELPFUL IN COMPARISON
The cost of materials, labour and overhead for every job or product in a department is available regularly and periodically, enabling the management to know the trend of cost and thus by suitable comparison, to control the efficiency of operations, materials and machines.
ASSISTANCE OF BUDGETARY CONTROL
The adoption of predetermined overhead rates in job costing necessitates the application of a system of budgetary control of overheads with all the advantages.
IDENTIFY SPOILAGE AND WASTAGES
Spoilage and defective work can be easily identified with specific jobs or products so that responsibility may be fixed on departments or individuals.
SUITABILITY
Job costing is particularly suitable for cost plus and such other contracts where selling price is determined directly on the basis of costs.
PROMPT RESULTS
The cost of material, labour and overhead for every job or product in a department is available daily, weekly or as often as required while the job is still in progress.
NO DELAY IN COST ASCERTAINMENT
On completion of a job, the cost under each element is immediately ascertained. Costs may be compared with the selling prices of the products in order to determine their profitability and to decide which product lines should be pushed or discontinued.
HELPFUL IN PLANNING
Historical costs for past periods for each product, compiled by orders, departments, or machines, provide useful statistics for future production planning and for estimating the costs of similar jobs to be taken up in future. This assists in the prompt furnishing of price quotations for specific jobs.
ANALYSIS OF VARIANCES IN COSTS
The actual overhead costs are compared with the overhead applied at predetermined rates; thus, at the end of an accounting period, overhead variances can be analyzed.
OBJECTIVES OF JOB COSTING
Job costing serves the following objectives :
1. It helps in finding out the cost of production of every order and thus helps in ascertaining profit or loss made out on its execution. The management can judge the profitability of each job and decide its future course of action.
2. It helps management in making more accurate estimates about the costs of similar jobs to be executed in future on the basis of past records. The management can conveniently and accurately determine and quote prices for orders of a similar nature which are in prospect.
3. It enables management to control operational inefficiency by comparing actual costs with the estimated ones.
REQUISITES OF JOB COSTING SYSTEM
- A sound system of production control
- An effective time booking system
- Clearly defined cost centre
- Appropriate overhead absorption rate, and
- Proper material issue pricing method.
JOB COSTING PROCEDURE
The following is the procedure adopted for costing purposes in a concern using job costing:
- Job Number:
When an order has been accepted, an individual work order number must be assigned to each such job so that separate orders are capable of being identified at all stages of production. Assignment of job numbers also facilities reference for costing purposes in the ledger and is conveniently short for use on various forms and documents.
- Production order:
The Production Control Department then makes out a production order thereby authorising to start work on the job. Several copies of production order are prepared, the copies often being in different colours to distinguish them more easily. These copies are passed on to the following:
(i) All departmental foremen concerned with the job;
(ii) Storekeeper for issuance of materials; and
(iii) Tool room-an advance notification of tools required.
The columns provided in the production order differ widely, depending largely upon the nature of production.
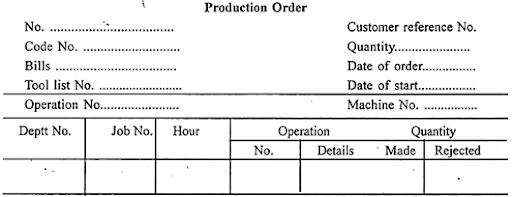
- Job Cost Sheet:
Job cost sheet is the most important document used in the job costing system. A separate cost sheet or card is maintained for each job in which all expenses regarding materials, labour and overheads are recorded directly from costing records. Job cost sheets are not prepared for specific periods but they are made out for each job regardless of the time taken for its completion. However, material, labour and overhead costs are posted periodically to the relevant cost sheet.
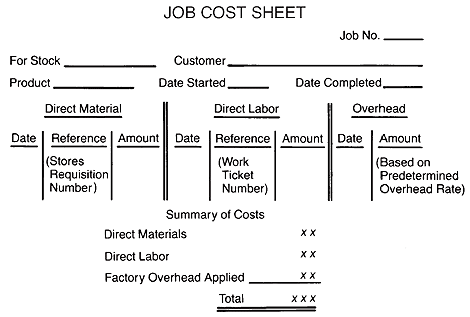
Costs for various jobs are collected on the following basis :
(a) Cost of materials: Materials requisition slips, bills of materials or materials issue analysis sheet.
(b) Cost of wages: Job cards, labour cost cards or wages analysis sheet.
(c) Direct expenses: Direct expense vouchers.
(d) Overheads: Overheads may be charged to each job on the basis of any of the methods of overhead absorption.
- Completion Report:
A completion report is sent to the costing department after the completion of job. The actual cost recorded in the job cost sheet is compared with the estimated cost. It will reveal the efficiency or inefficiency in operation. It is a guide to the future course of action.
- Profit or Loss:
Profit or loss on each job can be determined by comparing the actual cost with the price obtained.
LIMITATIONS OF JOB COSTING
Job costing suffers from certain limitations. These are as follows.
- It is said that it is too time consuming and requires detailed record keeping.
- Record keeping for different jobs may prove complicated.
- Inefficiencies of the organization may be charged to a job though it may not be responsible for the same.
- Job costing is comparatively more expensive as more clerical work is involved in identifying each element of cost with specific departments and jobs.
- With the increase in the clerical processes, chances of errors are enhanced.
- The cost as ascertained, even where they are compiled very promptly, are historical as they are compiled after incidence.
- The cost compiled under job costing system represents the cost incurred under actual conditions of operation. The system does not have any scientific basis.
CONCLUSION
In spite of the above limitations, it can be said that job costing is an extremely useful method for computation of the cost of a job. The limitation of time consuming can be removed by computerization and this can also reduce the complexity of the record keeping.