ELEMENTS OF COST
The elements of cost are the factors on the basis of which expenditure is incurred.
It may be defined as a group name of smaller costs of identical nature. Elements of cost make the analysis of the cost easy and facilitate maximum information regarding costs to the manufacturers.
COST
Cost refers to the expenditure incurred on producing the goods and services. It represents the sacrifice, foregoing or a release of something of value.
ACCORDING TO ICMA (Institute of Cost and Management Accountants), London
‘Cost is the amount of expenditure (actual or notional) incurred on or attributable to a given thing.”
Example: In manufacturing of automobiles, the expenditure incurred on its spare parts, painting and finishing, design, etc constitute the cost of the automobile.
Thus, cost can be said as the measure of resources given up to achieve an objective.
The following are the elements of the cost:
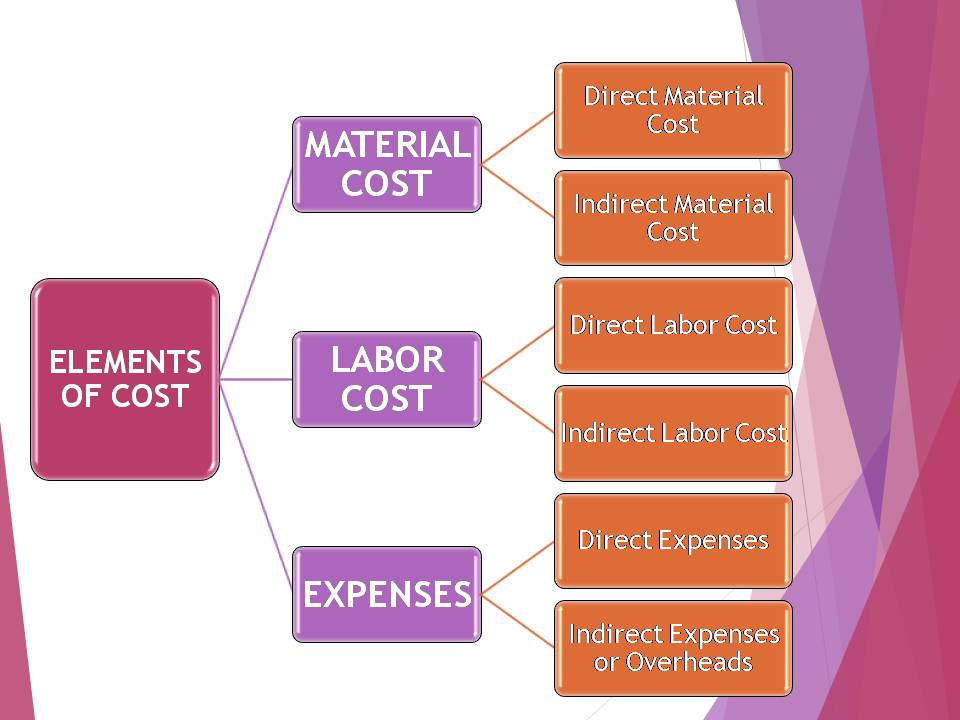
MATERIAL COST
It refers to the cost of the material that is supplied to the manufacturing unit for producing the finished product. Example: Cost of thread, nails, shoe polish, leather supplied to an undertaking engages in production of shoes constitute material cost.
Material cost can be classified as follows:
1.Direct material cost: Direct material cost is the cost of those materials that can be easily identifiable in the finished product. These costs can be attributable to the cost centers or cost units. The cost of such products is directly attributable to the cost of finished product.
Example:
- Cost of leather in shoes.
- Cost of glass in mirror.
- Cost of iron in machinery.
2.Indirect Material Cost: Indirect Material Cost is the cost which is not directly attributable to the finished product. These costs are not absorbed or apportioned by the cost units or cost centers directly. The cost of such material is not traceable in the finished product. These costs can also be known as non-identifiable or hidden costs.
Example:
- Cost of grease or lubricating oil used in maintenance of machinery.
- Fuel or electricity needed for generating power.
- Materials consumed for repair work.
- Dusters and brooms used for cleansing of factory.
LABOR COST
Labor cost refers to the cost of remuneration of the workers employed in an organization. It includes the amount of wages, salaries, perquisites, allowances etc. Labor cost is of two types:
1.Direct Labor Cost: These are also known as direct wages. This cost can be identified with and allocated to cost centers or cost units.
In case of manufacturing concern, it includes the remuneration paid for converting the raw material into finished products or for altering the construction, composition or condition of the product manufactured by an undertaking.
Example: Wages paid for spinning yarn in a spinning mill.
In case of service concern, direct labor cost refers to the wages paid to those who directly carry out or operate the service.
Example: Wages paid to the driver and conductor of a bus.
2.Indirect Labor Cost: These are also known as indirect wages. It refers to that part of labor cost which is not directly attributable to the cost centers or cost units. These are not apportioned to or absorbed by the cost centers or cost units.
Example: Salary paid to the manager, Salary paid to the guard of the office.
EXPENSES
Expenses refer to the cost of services provided to an undertaking and the notional costs of the use of the assets owned by the business house.
Example: Deprecation on building, plant and machinery etc.
The expenses are of two types:
1.Direct expenses: These expenses are also called chargeable expenses. These expenses can be directly identified to the cost centers or cost units.
Example:
- Carriage and freight paid on direct materials purchased.
- Import duty
- Octroi duty etc.
The aggregate of direct material cost, direct labor cost and direct expenses is known as Direct Cost.
2.Indirect Expenses or Overheads: Expenses which cannot be allocated to the cost centers or units but can be apportioned by them are known as overheads or indirect expenses.
Example:
- Rent, rates and taxes
- Repairs to machinery
- Factory lighting
- Office lighting
- Depreciation and insurance of showroom building etc.
The aggregate of indirect material cost, indirect labor cost and indirect expenses is known as Indirect Cost.
The indirect expenses or overheads can be further sub-divided into:
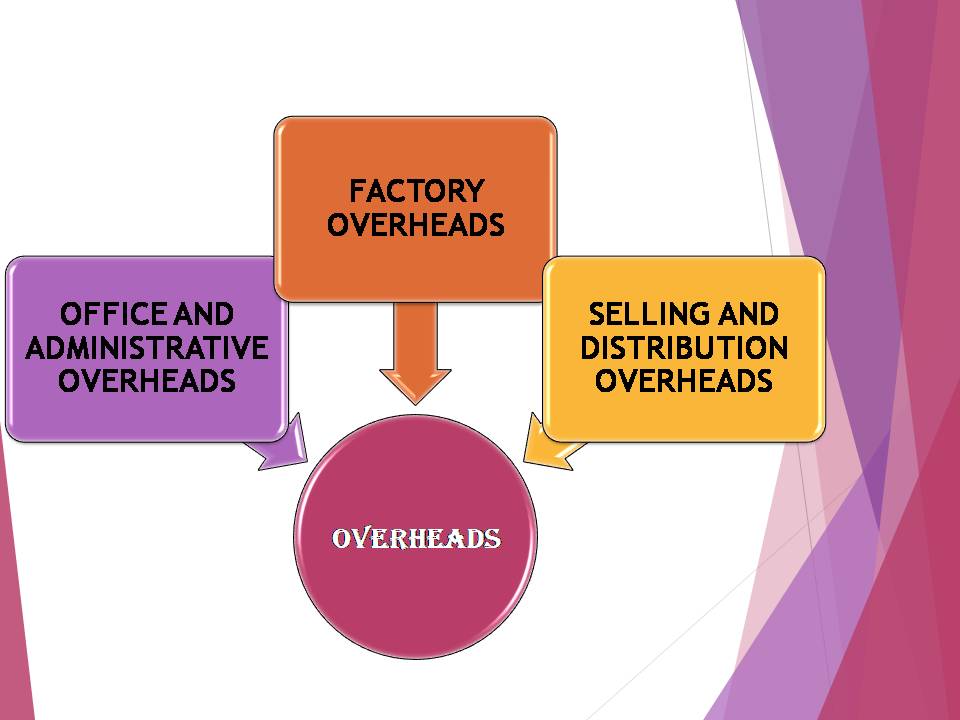
A)Factory overheads: It includes all the indirect costs incurred in factory in respect of manufacturing operations. It includes the cost of indirect materials and indirect labor.
Example: Cost of lubricating oil, coal, gas and fuel, wages of store-keeper, salaries of foremen, supervisors, factory rent etc.
B)Office and Administration Overhead: It refers to the general expenses and expenses of administration and control of business. It includes all the indirect costs relating to direction, guidance, management, control and administration of business concern.
Example: Salary of general manager, insurance expenses, office rents, office rates, office lighting etc.
C)Selling and Distribution overheads: These include all the indirect costs which are incurred for
- Promoting the sales
- Retaining the customers
- Providing after sale services to the consumers
- Raising the market share of the concern.
Example: Advertisement, salary of sales manager etc.
These costs play an important role in growing the business and its goodwill.
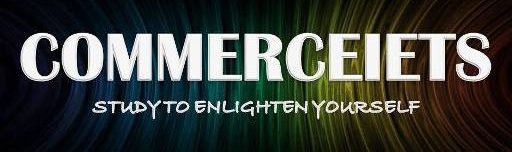