SCIENTIFIC MANAGEMENT
Scientific Management is defined as Application of science for each and every element of management. It means application of the scientific methods, tools and techniques by the managers to manage each operation effectively and efficiently. The Principles of Scientific Management insists on replacing the Rule of Thumb by the science which means decisions in the organization should not be taken on the basis of wills and wishes of the management instead should be taken on the basis of scientific studies conducted.
ACCORDING TO FREDRICK WINSLOW TAYLOR
“Scientific management means knowing exactly what you want men to do and seeing that they do it in the best and cheapest way.”
ACCORDING TO ASSOCIATION OF MECHANICAL ENGINEERS, USA
“It is the art and science of preparing, organizing and directing human effort applied to control the forces and utilize the materials of nature for the benefits of man.”
ACCORDING TO PETER F DRUCKER
“It is the operational study of work, the analysis of work into its simplest element and the systematic improvement of the workers’ performance of each element.
FREDRICK WINSLOW TAYLOR
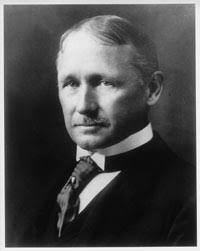
FW Taylor was born in 1856 in Philadelphia, USA. He served in three companies: Midvale Steel, Simonds Rolling Machine and Bethlehem Steel. He is known as Father of Scientific Management because of his following contributions:
- He emphasized on adoption of scientific methods to the problems of management.
- He wrote various books and articles such as ‘Shop Management (1930)’, ‘Principles of Scientific Management (1911)’, ‘Concrete Costs (1912)’, ‘Scientific Management (1913)’, ‘A Piece rate System (1895)’, ‘The Gospel of Efficiency(1911)’.
TECHNIQUES OF SCIENTIFIC MANAGEMENT

FUNCTIONAL FOREMANSHIP
This technique is an extension of principle of division of labor. As per this technique, the whole factory should be divided into two parts: Planning Department and Production Department. There should be minimum eight specialists to perform the activities of their expertise.
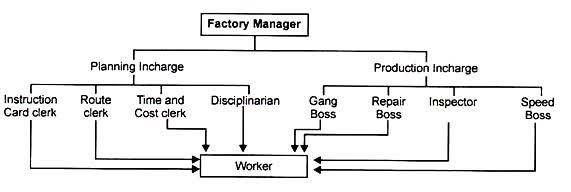
Planning Department: Under Planning Department there should be 4 specialists appointed such as:
- Route Clerk: The route clerk is a foreman responsible to fix up the steps for performing mechanical or manual job.
- Instruction Card Clerk: This foreman is responsible for giving general instructions necessary to carry on the job in a specified manner.
- Time and Cost Clerk: This foreman is responsible to fix up the time for starting and completion of job. He is also responsible for preparing the cost sheet for every job.
- Disciplinarian: This foreman is responsible for performance of job in orderly and systematic way.
Production Department: In Operations or Production Department, there should be 4 specialists enlisted below:
- Gang Boss: He arranges all the machines, tools and other resources required for performance of the job so that there should be no delay in getting the task completed.
- Speed Boss: This foreman ensures that the task is completed within the standard time.
- Repair Boss: This boss ensures that machines and tools are kept in the working conditions.
- Inspector: This boss keeps a check on quality control of the output.
Taylor was of the opinion that the appointment of these eight foremen ensures the smooth functioning of the factory.
STANDARDIZATION AND SIMPLIFICATION OF WORK
Standardization refers to setting up standards for each activity. It does not setting of standards for quality of product only but also setting the standards for size, type, weights and measures of output. The objectives of standardization are as follows:
- To reduce a given line of product to fixed type, size and characteristics.
- To allow the interchangeability of manufactured parts and output among different departments and branches.
- To maintain the quality standards.
- To set up performance standards for men and machines.
Taylor emphasized that various scientific studies like work study, method study, fatigue study methods should be adopted for setting up the standards.
The companies like Nokia, Apple, Nike, Videocon etc have also adopted the technique of standardization.
Simplification of work refers to elimination of unnecessary diversity of products, sizes and types. It means optimum utilization of resources i.e. men, machines and material through uninterrupted runs and fewer machine stoppages. It aims at discarding the unnecessary diversity of products.
Example: A paper manufacturing company in USA reduced its varieties from 2,000 to 200 which brought positive results for the company.
WORK STUDY
Under Scientific management, the management is responsible for determining the task for every employee which he performed in standardized working conditions. The standard work may be determined through proper investigation and taking into account average worker abilities.
According to Taylor, the best way of doing the work is that which requires least movement, cost and time. The best way of doing work can be determined by following studies:
Method Study: Under this study the best method of doing the job is to found out that will incur minimum cost and gives maximum benefit. There is detailed study of whole process of production to make improvements in material handling, transportation, inspection, storage etc. The objective of this study is to minimize the cost of production and maximize the quality and customer satisfaction.
Example: For production of shoes, there can be labor intensive method and machine intensive method. To find out which is best, management must evaluate the cost of production with both the methods and compare both the methods with the available resources of the company. The method which involves minimum cost and exploits maximum resources must be selected as the best method of production.
Ford Motors used this technique very successfully.
Time Study: The technique of time study involves determination of:
- The standard time required to perform the job.
- Setting up the target for workers.
- Determining the number of workers required to perform a job.
- Categorizing the workers in efficient and inefficient categories.
Taylor suggested that to set the standard time, the speed of an average worker should be observed for repeated times. Keeping the observed time in mind, the standard time should be set up.
Motion Study: This scientific technique is conducted with the objectives of:
- To determine the movements of workers when they are performing the job.
- To differentiate the productive and unproductive movements.
- For cutting down or eliminating the unproductive movements.
- To design the suitable equipment and tools to minimize the unproductive movement of workers.
Motion study is conducted before the time study. Both studies help in determining the best method of doing a job and standard time allowed for it.
Example: While observing an average worker, if it is observed that worker has to bend frequently to pick up the tools from the tool box placed under his table, then a stool can be placed near his seat to keep the tool box over it so that worker does not waste his energy in bending again and again. Same energy he can use for improving his production capacity or efficiency level.
Fatigue Study: Fatigue means tiredness. The fatigue study is conducted with the aim to determine:
- The frequency of rest intervals.
- The duration of rest intervals.
- The number of rest intervals.
A person is bound to get tired when he is performing the job for a longer period of time. There is always a need for rest interval. Taylor suggested that an average worker should be observed frequently. His efficiency levels when starts declining should be noted and on this basis rest intervals should be decided upon.
DIFFERENTIAL PIECE WAGE SYSTEM
This technique was introduced by FW Taylor to make a difference between efficient and inefficient employees. This technique insists on:
- Paying different rate of wage to efficient and inefficient employees.
- Extra wages paid to efficient employees will motivate them to remain efficient.
- Inefficient employees will work hard to become efficient and earn more.
- When payment is given according to number of units produced automatically the production will be maximized.
Thus, the worker who is doing less must be paid less. And the worker who is producing more must be paid more.
Example: Suppose the standard production rate is 10 units. A person producing standard output earn Rs 50 per unit, person producing more than standard output earns Rs. 60 per unit, person producing less than standard output earns Rs.40 per unit. Thus the wage pay as per differential piece rate system will be:
Employee producing standard output: 10*50= Rs.500
Employee producing more than standard output (say 12): 12*60= Rs. 720
Employee producing less than standard output (say 8 units): 8*40= Rs. 320
MENTAL REVOLUTION
Scientific management involves a complete mental revolution on the part of the workers and the employers. Scientific management can be implemented successfully only when there is complete mutual trust and understanding between workers and management. This technique aims at:
- Change in mental attitudes of workers and management towards each other.
- Cooperation between workers and management.
- Ruling out of suspicion or prejudice from the minds of workers and management to adapt systematic thinking.
Employers and employees should have positive attitude towards each other. Management Group should share the profits with Workers Group and in return workers group must give their best in operations. There should be paternalistic style of management.
Example: In Japanese companies, this principle is practiced as here managers treat workers as part of their family and workers do not show their agitation by going on strike rather they tie a black ribbon to show their dissatisfaction and gain sympathy of managers. Managers must work almost side by side with the workers, helping and encouraging them.