VARIANCE ANALYSIS
Variance Analysis is the analysis of variances arising in a standard costing system into their constituent parts. It is the analysis and comparison of the factors which have caused the differences between predetermined standards and actual results, with a view to eliminating inefficiencies.
ACCORDING TO I.C.M.A.
“Variance analysis is the resolution into constituent parts and explanation of variances”.
ACCORDING TO S.P.GUPTA
“Variance analysis is the measurement of variances, location of their root causes, measuring their effect and their disposition”.
Thus, variance analysis can be defined as the segregation of total cost variances into different elements in such a way as to indicate or locate clearly the cause for such variances and persons held responsible for them.
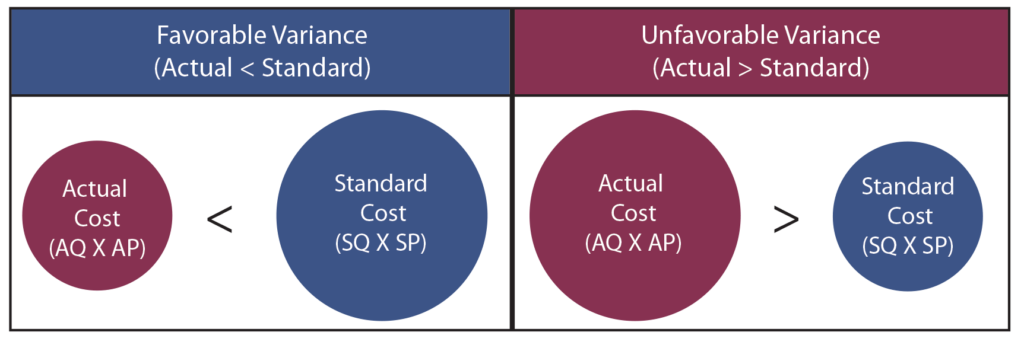
IMPORTANCE OF VARIANCE ANALYSIS
The following points depicts the importance of variance analysis for the management:
Budget vs. Actual Costs
Variance analysis is important to assist with managing budgets by controlling budgeted versus actual costs. In program and project management, for example, financial data are generally assessed at key intervals or milestones. For instance, a monthly closing report might provide quantitative data about expenses, revenue and remaining inventory levels. Variances between planned and actual costs might lead to adjusting business goals, objectives or strategies.
The Materiality Threshold
A materiality threshold is the level of statistical variance deemed meaningful, or worth noting. This will vary from company to company. For example, a sales target variance of Rs.100,000 will be more material to a small business retailer than to a national retailer accustomed to generating billions in annual revenues.
Relationships Between Variables
Relationships between pairs of variables might also be identified when performing variance analysis. Positive and negative correlations are important in business planning.
As an example, variance analysis might reveal that when sales for widget A rise there is a correlated rise in the sales for widget B. Improved safety features for one product might result in sales increases. This information might be used to transfer this success to other similar products.
Business Trend Forecasting
An important type of prediction is business forecasting. It uses patterns of past business data to construct a theory about future performance. Variance data are placed into context that allows an analyst to identify factors such as holidays or seasonal changes as the root cause of positive or negative variances.
For example, the monthly pattern of sales of television sets over five years might identify a positive sales trend leading up to the beginning of the school year. As a result, forecasts for television sales over the next 12 months might include increasing inventory by a certain percentage – based on historical sales patterns – in the weeks before the start of local universities’ fall term.
TYPES OF VARIANCES
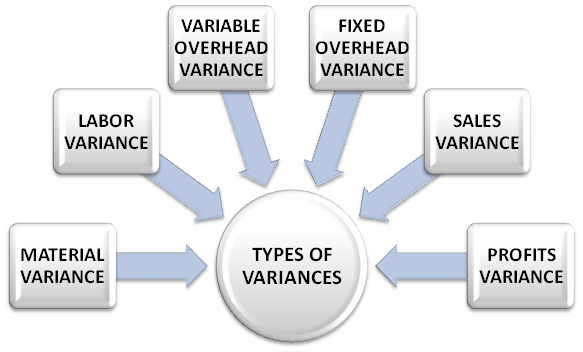
MATERIAL VARIANCES
For the purpose of material variance analysis, the following two types of standards need be fixed.
1. Material Price Standards:
Price factor is controlled by external factors. If the price changes during the period due to inflation, raise in prices of controlled items like cement, steel, etc., there is going to be wide variations.
Material prices are fixed keeping in mind the terms of contract of purchases, nature of items and other relevant factors. Some organizations have regular system of purchases (rate contract) for the whole period/year at predetermined price irrespective of the prevalent market rates.
2. Material Quantity Standards:
Quantity usage standards are set on the basis of various test runs and guidelines provided by R&D department or Engineering department and specifications on the basis of past experience. The standards should also take into consideration allowances for acceptable level of waste, spoilage, shrinkage, seepage, evaporation, leakage, etc.

Material Cost Variance
The material cost variance is also called ‘material total variance’ is the difference between standard direct material cost of actual production and the actual cost of direct material.
(Standard units x Standard price) – (Actual units x Actual price)
Material Price Variance
The material price variance is the difference between the standard price and the actual purchase price for each unit of material multiplied by the actual quantity of material purchased. It is preferable to base the price variance on the actual quantity of material purchased and not on the actual quantity used in order that price variances can be reported for control purposes.
Actual quantity (Standard price per unit – Actual price per unit)
Material Usage Variance
The material usage variance is the difference between the actual quantity of material used and the standard quantity of material that should be used for actual production, multiplied by the standard price per unit of material.
Standard price per unit (Standard quantity – Actual quantity)
Material usage variance is further segregated into (a) Material mix variance, and (b) Material yield variance.
Material Mix Variance
If a process uses several different materials which could be combined in a standard proportion, a mix variance can be calculated which shows the effect on cost of variances from the standard proportion. There are two recognized ways of calculating this mix variance.
Material Mix Variance= Standard price (Revised standard quantity – Actual quantity)
Revised Standard Quantity= (Total quantity of actual mix/Total quantity of standard mix) x Standard quantity
Material Yield Variance
Apart from operator or machine performance, output quantities produced are often different to those planned, e.g., this arises in chemical plants where plant should produce a given output over a period for a given input but the actual output differs for a variety of reasons. Material yield variance is the difference between the standard yield of the actual material input and the actual yield, both valued at the standard material cost of the product.
Standard cost per unit (Standard output for actual mix – Actual output)
LABOUR VARIANCES
Normally it is taken that labour is a variable cost but at times it becomes fixed cost as it is not possible to remove or retrench in case of fall/stoppage in production.
Labour Rate Standard and Grades of Labour:
This is basically dependent on the agreement with the labour unions or rate prevalent in the particular area or industry.
Labour Efficiency Standard:
The labour (quantities) efficiency means the number of hours that the appropriate grade of worker will take to perform the necessary work. It is based on actual performance of worker or group of workers possessing average skill and using average effort while performing manual operations or working on machine under normal conditions. The standard time is fixed keeping in mind the past performance records or work study. This is on the basis that is acceptable to the worker as well as the management.
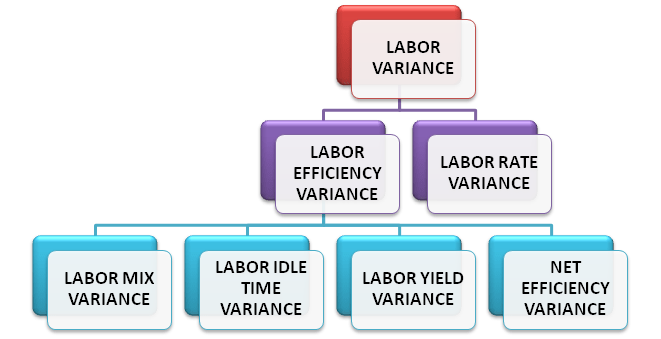
Labour Cost Variance
The labour cost variance is also called’ labour total variance’ is the difference between the standard direct labour cost and the actual direct labour cost incurred for the production achieved.
(Standard labour hours produced x Standard rate per hour) – (Actual direct labour hours x Actual rate per hour)
or Standard cost for actual output – Actual cost
Labour Rate Variance
The labour rate variance is the difference between the actual direct labour rate per hour and the standard direct labour rate per hour, multiplied by the actual hours paid, i.e., the rate per hour paid to the direct labour force more or less than standard use of higher/lower grade of skilled workers than planned or wage inflation causes this variance.
Actual time (Standard rate – Actual rate)
Labour Efficiency Variance
The labour efficiency variance is the difference between the actual hours taken to produce the actual output and the standard hours that this output should have taken, multiplied by the standard rate per hour. The possible cause for this variance is due to use of higher/lower grade of skilled workers than planned or the quality of material used, errors in allocating time to jobs.
Standard rate (Standard time for actual output – Actual time)
The labour efficiency variance can be segregated into the following:
Labour Mix Variance
The labour mix variance arises due to change in composition of labour force.
Labour Mix Variance= Standard rate (Revised standard time – Actual time)
Revised Standard Time= Total actual time/Total standard time x Standard time
Labour Yield Variance
The labour yield variance arises due to the difference in the standard output specified and the actual output obtained.
Standard cost per unit (Standard output for actual time – Actual output)
Idle Time Variance
The idle time variance represents the difference between hours paid and hours worked, i.e., idle hours multiplied by the standard wage rate per hour. This variance may arise due to illness, machine breakdown, holdups on the production line because of lack of material.
Idle hours x Standard rate
Net Efficiency Variance
This variance is calculated after deducting idle hours from actual hours. The efficiency variance less idle time variance is called ‘net efficiency variance’.
Standard rate ( Standard time for actual output – Actual time worked)
or Standard rate (Standard time – Actual hours paid – Idle time)
VARIABLE OVERHEAD VARIANCES
For fixation of costs for overheads, a survey of overheads will be necessary and with the data available for budgetary control, the overheads will be charged to various cost centres/products etc. on the basis of standard costs. For this, after dividing the overheads into fixed and variable the calculation of standard overhead rate for each cost centre/product is done.
The number of hours representing the capacity to manufacture is to be reduced by various idle facilities, etc. The choice of method of absorption (direct wage rate or machine hour) will depend upon the circumstances. The main object is to establish a normal overhead rate based on total factory overhead at normal capacity volume.
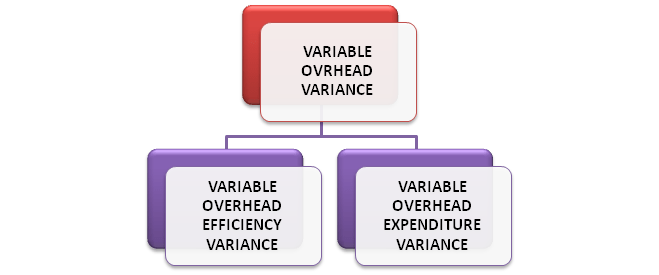
Variable Overhead Cost Variance
The variable overhead cost variance represents the difference between the standard cost of variable overhead allowed for actual output and the actual variable overhead incurred during the period. The variance represents the under absorption or over absorption of variable overheads.
(Actual output x Standard variable overhead rate p.u.) – Actual variable overhead cost
or (Standard hours for actual output x Standard variable overhead rate per hour) – Actual variable overhead cost
Variable Overhead Expenditure Variance
It is the difference between the actual variable overhead rate per hour and the standard variable overhead rate per hour multiplied by the actual hours worked. The actual hours worked must be used not the actual hours paid because the latter may include idle time and it is usually assumed that variable overhead will not be recovered in idle time.
(Standard variable overhead rate x Budgeted output) – Actual variable overheads
or (Standard hours for budgeted output x Standard variable overhead rate per hour) – Actual variable overheads
or Budgeted variable overheads – Actual variable overheads
Variable Overhead Efficiency Variance
The variable overhead efficiency variance is calculated by taking the difference in standard output and actual output multiplied by the standard variable overhead rate.
Standard variable overhead rate (Standard output – Actual output)
FIXED OVERHEAD VARIANCES
Fixed overhead represents all items of expenditure which are more or less remain constant irrespective of the level of output or the number of hours worked.
The fixed overheads variances are classified as follows:
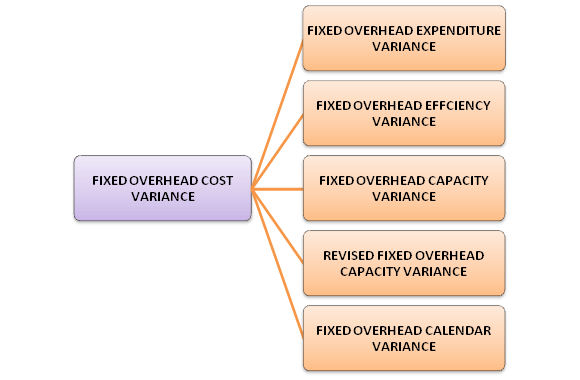
Fixed Overhead Cost Variance
The fixed overhead cost variance represents the under/over absorbed fixed production overhead in the period. This under/over absorbed overhead may be due to differences between actual and budgeted fixed overheads, i.e., expenditure variances, and/or differences between the actual and budgeted levels of activity i.e., volume variances.
(Actual output x Standard fixed overhead rate per unit) – Actual fixed overheads
or (Standard hours for actual output x Standard fixed overhead rate per hour) – Actual fixed overheads
or Recovered fixed overheads – Actual fixed overheads
Fixed Overhead Expenditure Variance
This variance is also called ‘budget variance’, obtained by comparing the total fixed overhead cost actually incurred against the budgeted fixed overhead cost.
Budgeted fixed overheads – Actual fixed overheads
Fixed Overhead Volume Variance:
The volume variance is computed by taking the difference between overhead absorbed on actual output and those on budgeted output.
(Actual output x Standard rate) – Budgeted fixed overheads
or Standard rate (Actual output – Budgeted output)
or Standard rate per hour (Standard hours produced – Budgeted hours)
Fixed Overhead Efficiency Variance
The efficiency variance arise due to the difference between budgeted efficiency to production and the actual efficiency is achieved.
Standard rate (Actual output in units – Standard output in units)
or Standard rate per hour (Actual hours worked – Standard hours for actual output)
Fixed Overhead Capacity Variance
The capacity variance represents the part of volume variance which arise due to working at higher or lower capacity than standard capacity
Standard rate (Budgeted quantity – Standard quantity)
Revised Fixed Overhead Capacity Variance
The revised capacity variance is calculated as follows:
Standard fixed overhead rate (Revised budgeted quantity – Standard quantity)
Fixed Overhead Calendar Variance
The calendar variance arise due to the volume variance which is due to the difference between the number of working days anticipated in the budget period and the actual working days in the period to which the budget is applied.
Standard fixed overhead rate (Budgeted quantity – Revised budgeted quantity)
SALES VARIANCES
All of the variances discussed previously have been concerned with costs; the effects on profits due to adverse or favourable variances affecting direct materials, direct labour or overheads. Some companies calculate cost variances only, but to obtain the full advantages of standard costing, it is required to calculate sales variances.
Sales variances affect a business in terms of changes in revenue: changes which have been caused either by a variation in sales quantities or in sales prices.
There are two distinctly separate systems of calculating sales variances, which show the effect of a change in sales as regards:
(i) Sales margin variance (on the basis of profit),
(ii) Sales value variance (on the basis of turnover).
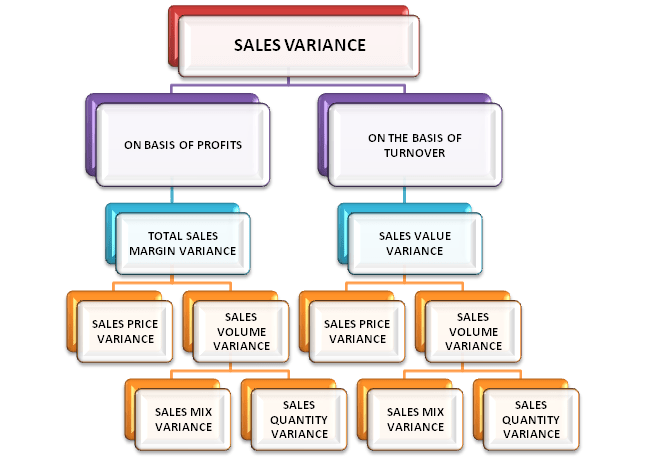
Sales Variances Based on Profit:
The sales variances based on profit are also called ‘sales margin variances’ which indicated the deviation between actual profit and standard or budgeted profit:
Total Sales Margin Variance
This variance takes into account the difference between actual profit and standard or budgeted profit.
Actual profit – Budgeted profit
or (Actual quantity of sales x Actual profit per unit) – (Budgeted quantity of sales x Budgeted profit p.u.)
Sales Price Variance
The price variance is the difference between standard price of the quantity of sales effected and the actual price of those sales.
Actual quantity of sales (Actual profit per unit – Standard profit per unit)
or (Actual quantity of sales x Standard price) – (Actual quantity of sales x Actual price)
Sales Volume Variance
It represents the difference between the actual units sold and the budgeted quantity multiplied by either the standard profit per unit or the standard contribution per unit. In absorption costing standard profit per unit is used, but in marginal costing, standard contribution per unit must be used.
Standard profit p.u. (Actual quantity of sales – Standard quantity of sales)
or Standard profit on actual quantity of sales – Standard profit on standard quantity of sales
Sales volume variance can be further segregated into (a) Sales mix variance and (b) Sales quantity variance as given below:
Sales Mix Variance
The sales mix variance arises when the company manufactures and sells more than one type of product. This variance will be due to variation of actual mix and budgeted mix of sales.
Standard profit per unit (Actual quantity of sales – Standard proportion for actual sales)
Or Standard profit – Revised standard profit
Sales Quantity Variance
The sales quantity is the difference between the budgeted profit on budgeted sales and expected profit on actual sales.
Standard profit per unit (Standard proportion for actual sales – Budgeted quantity of sales)
or Revised Standard Profit – Budgeted Profit
or Budgeted margin per unit on budgeted mix (Total actual quantity – Total budgeted quantity)
Sales Variances Based on Turnover
The sales variances based on turnover are classified as follows:
Sales Value Variance
(Actual quantity x Actual selling price) – (Standard quantity x Standard selling price)
Sales Price Variance
Actual quantity (Actual selling price – Standard selling price)
Sales Volume Variance
Standard selling price (Actual quantity of sales – Standard quantity of sales)
Sales Mix Variance
Standard value of actual mix – Standard value of revised standard mix
Sales Quantity Variance
Standard selling price per unit (Standard proportion for actual sales quantity – Budgeted quantity of sales)
or Revised standard sales value – Budgeted sales value
PROFIT VARIANCES
The profit variances are classified as follows:
Profit Value Variance:
Budgeted profit – Actual profit
Profit Price Variance:
Actual quantity (Standard rate of profit – Actual rate of profit)
Profit Volume Variance:
Standard rate of profit (Budgeted quantity – Actual quantity)
Profit Mix Variance:
Revised standard profit – Standard profit
Profit Quantity Variance:
Budgeted profit – Revised standard profit.
JOIN THE CHANNEL ON TELEGRAM
CONNECT ON LINKEDIN